Descripción del modelo planteado:
Estamos simulando una producción de artículos de moda donde es necesario hacer cambios
de productos en una línea de producción para atender al mercado. Cuando se operan estos
cambios existe una perdida de producción durante los primeros días en función de los
tiempos de set-up que son clasificados en : Alteración en el lay-out, ajustes en los equipos,adecuación de los trabajadores a los nuevos materiales y aprendizaje de nuevas
operaciones. Estos factores interfieren reduciendo el ritmo normal del trabajo durante un
determinado periodo de tiempo volviendo al normal y quedándose estables a lo largo del
tiempo. Los factores ya están considerados en la curva de eficiencia inicial representada en
el modelo.Nuestro objetivo aquí es encontrar cual es la cantidad mínima de producción por
producto que deberá ser planeada de forma que los tiempos de set-up no nos causen
perjuicios con relación al costo pré-establecido, es importante mantener la flexibilidad no
implantando lotes de producción demasiado grandes que también aumentan las existencias.
Para encontrar el punto ideal haremos análisis de sensibilidad estudiando las variaciones en
cada una de las simulaciones, conciliando costos previstos con cantidad ideal de
producción.
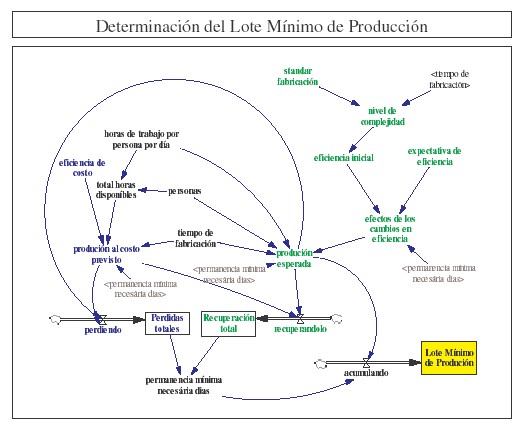
Explicación del Modelo y sus ecuaciones:
Para mejor entendimiento de las ecuaciones dividimos el modelo en dos partes que están
pintadas en verde y en azul, siendo la primera producción esperada y la otra producción
al costo previsto.
Las variables que están en negro son comunes a las dos partes del modelo.
Abajo se explican las ecuaciones que fueron consideradas para montarlo y un estudio de
sensibilidad para entender los efectos que causan.
Ecuaciones utilizadas:
Standard de fabricación
Es el tiempo en horas decimales por unidad de fabricación que servirá de base para el
cálculo de la complejidad cuando hay un cambio de un artículo para otro.
Nivel de complejidad
El modelo propone 4 tipos de complejidad que determinan las eficiencias iniciales.
Cuanto mayor sea la complejidad, menor será la eficiencia inicial, conforme la tabla
eficiencia inicial.
Eficiencia Inicial
Eficiencia inicial es el rendimiento inicial que el grupo de personas alcanza cuando
empieza a producir un artículo nuevo, es decir que existen tiempos de set-up como cambios
de lay-out, ajustes de equipos, adecuación a nuevos materiales, aprendizaje de nuevas
operaciones que interfieren reduciendo el ritmo normal del trabajo en el inicio de un nuevo
artículo, pero a lo largo del tiempo aumentan el rendimiento y se estabiliza.
Expectativa de eficiencia
Es la eficiencia posible de alcanzar a lo largo del tiempo, o sea es 100% de la capacidad
disponible para cualquier artículo, claro que los artículos con mayor complejidad tardarán
mas tiempo en llegar al 100% que los de menor complejidad
Efectos de los cambios en eficiencia
Es la curva de crecimiento de eficiencia inicial en función de la complejidad del artículo.
Tiempo de fabricación
Se cambia cuando
queremos simular otro artículo, que tenga otro tiempo.
La división de los recursos disponibles por el tiempo de fabricación del artículo nos resulta en la capacidad de producción al 100%, o sea, sin set-up, también se utiliza para definir el nivel de complejidad del modelo como ya explicado hacia arriba.
Producción esperada
Esta ecuación tiene el objetivo de calcular cual es la producción posible por día,
considerando los recursos que tenemos disponibles y utilizando la eficiencia inicial, de
acuerdo con el nivel de complejidad de cada uno de los artículos.
Cuando multiplicamos la producción por la variable permanencia mínima necesaria, en
la verdad, estamos eligiendo solo el periodo que es necesario para que el grupo de trabajo
alcance una producción acumulada igual o mayor que a la producción al costo previsto.
Permanencia mínima necesaria es una de las últimas ecuaciones que se hacen, pero vuelve
hacia atrás para elegir una parte de la producción conforme explicado hacia arriba.
Recuperando
Esta condición que se propone es para saber a partir de cuando la producción esperada del
artículo que está siendo simulado es mayor que la producción al costo previsto, solo nos
interesa saber cuando es mayor, o sea si no es mayor queremos que en este día se coloque
cero.
Recuperación total
Acumula los valores de producción esperada, como ya se explico, son únicamente los que
son mayores que la producción al costo previsto.
Ahora vamos a determinar la producción al costo previsto, utilizaremos algunos datos que
son comunes a las dos partes tanto para la producción esperada como para la producción
al costo previsto, los datos son: personas, horas de trabajo por persona por día,
permanencia mínima necesaria días, tiempo de fabricación.
Estas informaciones están en negro en el modelo, solo el tiempo de fabricación está en rojo
pues es la variable que cambiamos para hacer simulaciones de complejidad y de
producción cuando cambiamos de un artículo para otro.
Horas de trabajo por persona por día = 8 horas es una constante
Personas = 8 personas
Se puede cambiar para aumentar los recursos y en consecuencia la producción si queremos.
Total de horas disponibles
Es la capacidad disponible para la producción
Eficiencia de costo
Este parámetro nos informa que el costo del producto tiene una eficiencia de 0.70, o sea, se
espera que en lo mínimo el grupo produzca lo equivalente al 70% de los recursos
empleados.
Caso altere esta variable tendremos:
1) Si hacemos la previsión de costos a una eficiencia mayor que 0.70 tendrá una
previsión de costos menor, mas serán necesarios mas días para alcanzar el lote
mínimo. Cuanto mayor el lote mínimo menos flexibilidad y mayores existencias.
2) Si prevemos una eficiencia menor que 0.70, pasará lo opuesto al íten 1, o sea,
mayores costos, con posibilidad de menores existencias y con lote mínimo de
producción menor, quiere decir que tenemos mas flexibilidad.
Podremos entender mejor estos efectos en la análisis de sensibilidad después de las
explicaciones de las ecuaciones.
Producción al costo previsto
La primer parte de la ecuación (total de horas disponibles* eficiencia de costos)/ tiempo
de fabricación, define la capacidad de producción de los recursos utilizados trabajando a
una eficiencia pré-establecida, o sea, un standard de producción.
En la segunda parte de la ecuación utilizamos la variable permanencia mínima necesaria
para criar el mismo efecto que ya fue explicado en producción esperada hacia arriba.
Perdiendo
El raciocinio es el contrario al formulado en recuperando, o sea, aquí solo nos interesa las
cantidades de producción que sean menores que las cantidades en producción al costo
previsto, el resultado es negativo.
Perdidas Totales
Acumula los valores negativos de producción al costo previsto en perdiendo , como ya se
explico, son únicamente los que son menores que la producción esperada.
Permanencia mínima necesaria días
La condición que se propone es saber cuando la producción esperada acumulada será
mayor o igual que la producción al costo previsto acumulada. La identificación ocurre
cuando aparece el primer cero (0), o sea, en cuanto la producción esperada sea menor que
la producción al costo previsto el registro que aparecerá es el uno (1).
Lo que buscamos aquí es saber cuantos días seguidos sin cambios es necesario para
recuperar las perdidas de producción esperada por los tiempos de set-up.
Acumulando
Estamos eligiendo los valores de producción esperada que serán sumados para determinar
el tamaño del lote mínimo.
Lote Mínimo de Producción
Es la cantidad mínima que deberá ser planeada para la producción de un determinado
artículo de forma que no haya perjuicios en función de los tiempos de set-up.
Este es el resultado que el modelo busca encontrar, para cada artículo que se deseé simular.
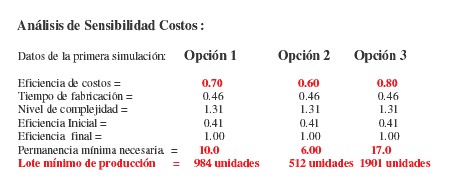
Conclusiones
Se estudian diferentes opciones.
La opción 3 tiene el menor costo pero es la peor en flexibilidad y habrán aumentos de
existencias, puede haber problemas para atender el mercado si este quiere diversificación y
solo es recomendable en los días de hoy cuando la margen de logro está muy apretada, o
sea la competencia es muy grande y el producto tiene como atractivo el precio.
La opción 2 es la mas cara pero es muy flexible y habrán poco stock, si el modelo tiene un
valor agregado que le permita absorber los costos de fabricación y aún tener garantizado la
margen de logro requeridas por los accionistas de la empresa, es una alternativa a ser
implementada.
La opción 1 es intermedia y deberá ser analizada junto a las otras dos.
(*) Puede solicitar información más detallada de este trabajo al autor